Твердомеры - разновидности и принцип действия
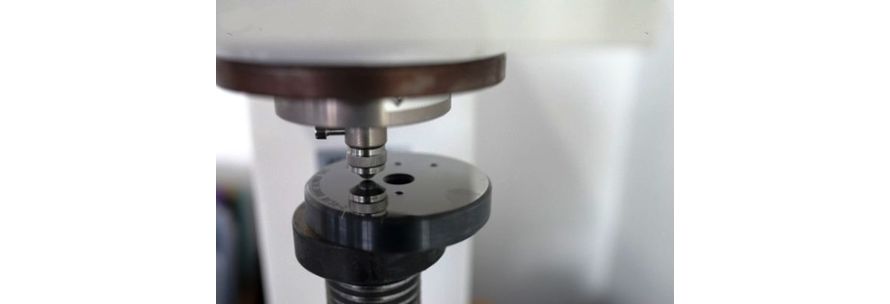
Одним из важных показателей, от которого зависит срок службы произведенного оборудования, деталей, комплектующих, а также безопасность, например при эксплуатации транспортных средств, станочного оборудования, деталей машин, является твердость.
Это касается множества направлений. Мягкие диски автомобиля из дешевой стали или сплавов быстро погнутся, как и кузов автомобиля пострадает при аварии. Трубопровод должен выдерживать давление жидкости или газа и не деформироваться, как и станина многотонного пресса.
Также нужно тестировать на твердость и неметаллические материалы: резинотехнические изделия, пластик, дерево, чтобы понимать, как они себя поведут в той или иной ситуации, при необходимости внести изменения в техпроцесс или заменить материал на более твердый.
Чтобы измерить этот параметр, уже множество десятилетий разработан целый ряд специализированых приборов, объединенных общим названием – твердомер.
При выборе следует исходить из специфики производства, требований к материалам, месту измерения (в пределах помещениях или нужно портативное устройство), весу объекта, габаритов, конструктивных особенностей и т.д.
Что такое твердомер
Это прибор, производящий силовое воздействие на испытуемый объект (разрушающее или неразрушающее), в результате чего фиксируется значение твердости, как результат от указанного воздействия в зависимости от методики и применяемой шкалы.
Но сначала дадим определение.
Это способность материала сопротивляться в локальной области проникновению в него более твердого тела. Чем больше нужно усилия приложить к последнему, и чем больше потребуется для этого времени, тем выше твердость исследуемого вещества.
Устройство
- Корпус. Должен выдерживать нагрузки и не терять своих качеств со временем. Имеется в виду, что крепежные элементы не должны разбалтываться, элементы конструкции раскалываться, сварные швы не расходиться и т.д., поскольку прилагаемое давление составляет десятки килограммов. И так множество раз в день, в зависимости от загрузки соответствующей лаборатории. Хотя существуют твердомеры и в виде портативного инструмента.
- Наковальня. Это площадка для размещения исследуемой детали.
- Индентор. Эта главный рабочий компонент. Он может быть разной формы, в зависимости от метода измерения, но должен иметь строго заданные параметры, чтобы погрешность не выходила за заданные пределы.
- Датчик. Формирует аналоговую величину, пропорциональную твердости.
- Электронная схема управления. Переводит полученную от сенсора величину в цифру и выводит на дисплей.
В более дорогих твердомерах есть встроенная память и возможность передавать полученные данные на компьютер.
Вся конструкция должна размещаться на горизонтальной ровной поверхности.
Корпусные элементы, а также площадка для помещаемых образцов и все подвижные детали прибора изготовлены из высококачественной стали и прочной пластмассы.
Что касается эксплуатационных параметров переносных моделей, которые функционируют в непростых “полевых условиях”, к ним дополнительно предъявляются требования по герметичности и защите от царапин, толчков и ударов.
Какие бывают измерители твердости
Методы и шкалы различные, но если говорить укрупненно, то все приборы для измерения твердости, работают по похожему принципу – это контакт тестируемой детали с индентором при строго заданных (нормированных) показателях нагрузки и временных интервалах.
Следует отметить, что в отличие от подавляющего большинства измерительных устройств, которые делятся на бытовые и профессиональные, для твердомеров такого разделения нет, поскольку в домашних условиях твердость практически не измеряют и сфера применения лежит исключительно в области производства, контроля качества, дефектоскопии и т.д.
Роквелл
Способ был предложен еще в начале XX века. Этот вид назван по имени их создателей и получил широкое распространие в виду его простоты, высокой повторяемости и достаточно быстрой скорости. Первоначальная потребность в измерений была вызвана контролем твердости подшипников. В 1919 году Роквеллы получили патент на этот метод.
Используется 2 вида конденторов:
- шарик из карбида вольфрама, что позволяет его использовать для большинства материалов, даже достаточно твердых, а также могут использоваться шарики из закаленной стали;
- алмазный наконечник с окончанием в виде конуса.
Нагрузки на измеряемый объект составляют 60, 100 и 150 кгс. Но сначала прилагается малая нагрузка – 10 кгс. Жесткий наконечник проникает на разную глубину в зависимости от твердости образца. Как определяется результат ? Как относительная величина – разница между предварительной и основной нагрузкой.
Существуют 2 важных требования:
Во-первых, чтобы деталь не раскололась: ее толщина должна быть в десять и более раз больше, чем глубина проникновения в нее индентора.
Во-вторых, расстояние между центрами двух соседних отпечатков должно должно превышать 3 их диаметра, поскольку пластическая деформация после первого измерения может влиять на последующие замеры.
В зависимости от применяемого материала шарика, конуса и выбранной загрузки, различаются шкалы: HRA, HRB, HRC, и далее вплоть до HRT.
Чем еще хороши измерители твердости Роквелла, так это отсутствием необходимости измерять диаметр отпечатка, что следует делать очень точно, это требует оптических инструментов и значительно увеличивает время для анализа.
Бринель
Метод основан на вдавливании высокотвердого шарика-индентора с образованием следа (отпечатка), а значит относится к разрушающим. Назван по имени создателя – инженера Бринеля и был разработан первым в мире.
Подходит для цветных металлов, мягких сплавов (кроме закаленной стали), дерева, меди, алюминия, дюрали, нержавейки, то есть для широкого спектра метариалов, применяемых в строительстве и промышленности. Отпечатки получаются с достаточно высокой степенью повторяемости и воспроизводимости.
Перед началом теста необходимо определиться как с прилагаемой нагрузкой, так и диаметром шарика, в зависимости от исследуемых материалов. Также большое значение играет время анализа.
Существует ряд ограничений при измерениях по методу Бринеля, причем их перечень больше, чем по Роквеллу:
1 | Диаметры полученных отпечатков должны находиться в границах 0,2D<d<0,6D, где D-диаметр шарика |
2 | Толщина образца не должна быть меньше чем 10-кратная глубина отпечатка |
3 | Расстояние между центрами ближайших отпечатков или краем исследуемого предмета не должны быть меньше чем 4D |
4 | Время выдержки после приложения нагружки: для сплавов и цветных металлов: 10-180с, для черных металлов (сталь, чугун): 10-15 сек |
5 | Поверхность должна быть ровной и очищенной, без окалины, сколов, трещин |
6 | Предельная величина твердости не должна быть больше 450 НВ |
Виккерс
Также используется для испытаний металлов и сплавов, и востребован в металлургической промышленности, при проведении расследований и испытаний, когда есть сомнения, что твердость не отвечает заданным значениям.
В этом варианте индентор выполнен в виде пирамиды, где углы между гранями составляют 136°. Пирамида вдавливается в анализируемый образец.
Поскольку отпечаток здесь не круглый, а ромбовидный, результат рассчитывается по следующей формуле: HV (обозначение измерения твердости по Виккерсу) = 1.854∙F/d2, где d- диагональ ромба, а F- величина силы.
Поскольку следы могут быть очень мелкими, для точного опредлеления размеров отпечатка, потребуется микроскоп - играет роль каждая сотая или даже тысячная доля миллиметра.
Твердомеры виккерса хороши своей универсальностью и широким пределом измерения и очень удобны например для анализа заготовок с тонким слоем напыления, которое отличается по твердости от основы, например для азотированных, анодированных деталей, обработанных методом гальванизации.
Но существуют у измерителей по Викерсу и недостатики:
- высокие требования к качеству поверхности. Причем чем на меньшую глубину проникает индентор, чем больше погрешность, если например пирамида попадет на скрытую микрораковину (пустоту - например если при выплавке остался пузырек газа), поскольку размеры дефекта соизмеримы с размерами отпечатка;
- Зависимость между прилагаемым усилием и полученной величиной.
Шор
Здесь применена другая методика, отличная от выше перечисленнях. Падающий с высоты боек при контакте с деталью, отскакивает обратно, вверх. Величина отскока пропорциональна твердости, поскольку в момент соприкосновения происходит локальная упругая пластическая леформация, материал снова распрямляется, принимая исходную форму и выталкивает индентор.
Это неразрушающий метод и используется для резины, каучука и других неметаллов.
Метод не отличается восокой точностью, поскольку высота отскока определяется и другими параметрами: ровностью поверхности, толщиной, зернистостью, шероховатостью.
Обозначение показателя по Шору “HS”.